From the early days of the automobile until now, tires have seen many technological advancements. Improvements in raw materials and chemical compounds have led to tires that perform more effectively.
Whether it’s compounds offering better grip in snow and ice or compounds providing improved wet handling, technology continues to enhance tire performance. Innovations in tread patterns, sidewall design and overall tire construction have made today’s higher-performing tires more reliable than ever before. Tire manufacturers work hand in hand with vehicle designers to engineer tires for the future.
One of the most comprehensive technological innovations of the modern tire era is run-flat tire technology. Run-flat technology allows drivers who sustain air loss due to a puncture or cut in their tire to drive approximately 50 miles at 50 m.p.h. so they can reach a safe location to change the tire.
Elements contributing to modern tire technology
Rubber is the main raw material used in manufacturing tires, and both natural and synthetic rubber are used. Natural rubber is found as a milky liquid in the bark of the rubber tree, Hevea Brasiliensis.
The other primary ingredient in tire rubber is carbon black. Carbon black is a fine, soft powder created when crude oil or natural gas is burned with a limited amount of oxygen, causing incomplete combustion and creating a large amount of fine soot. So much carbon black is required for manufacturing tires that rail cars transport it and huge silos store the carbon black at the tire factory until it is needed.
Sulfur and other chemicals are also used in tires. Specific chemicals, when mixed with rubber and then heated, produce specific tire characteristics such as high friction (but low mileage) for a racing tire or high mileage (but lower friction) for a passenger car tire. Some chemicals keep the rubber flexible while it is being shaped into a tire while other chemicals protect the rubber from the ultraviolet radiation in sunshine.
However, constant improvements in rubber chemistry and tire design are creating exciting new tires that offer greater mileage and improved performance in extreme weather conditions. Manufacturers now offer tires estimated to last up to 80,000 miles. Treads, designed and tested by computer, now feature unique asymmetrical bands for improved traction and safety on wet or snowy roads.
Tire design engineers are also experimenting with non-pneumatic tires that can never go flat because they don’t contain air under pressure. One such non-pneumatic tire is simply one slab of thick plastic attached to the wheel rim. The plastic curves out from the rim to a point where a rubber tread is secured to the plastic for contact with the road. Such a tire offers lower rolling resistance for greater fuel economy and superior handling because of a greater area of contact between tread and road.
According to Mallesh Kumar at ZAFCO Low Rolling resistance, higher fuel efficiency, less carbon emission, low cost per kilo meter are among the elements contributing to the modern tire technology.
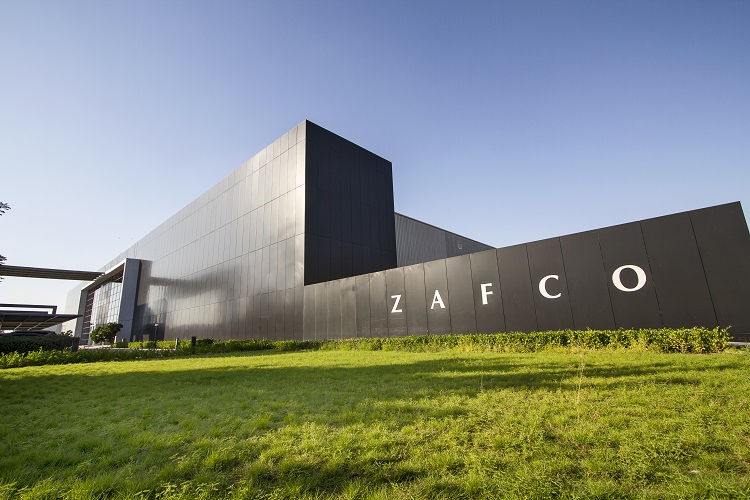
ZAFCO is one of the leading importers and exporters of automotive tires, batteries, and lubricants and operates internationally to cater the needs of hundreds of customers spread across all six continents.
Tire challenges in the African roads
When it comes to tires, the African continent is one of the fastest growing markets for the global tire industry. The rapid growth of the middle class in many African countries has pushed demand for automobiles to an all-time high – in turn creating a growing market for all kinds of tires: passenger car tires, off-the-road tires, industrial tires, agricultural tires, truck, bus and trailer tires as well as motorcycle and bicycle tires.
Even so, tire industry is faced with one great obstacle called roads. Africa’s roads are notorious and more than half of them are unpaved. This has greatly hinder tire growth in Africa given that manufacturing process improvements have largely been spurred on by environmental concerns. Moreover, growing demand has resulted in the setting up of new manufacturing units that are more capable of handling technology and new equipment. Automation advances have also helped to a significant extent.
“Road conditions, terrain, maintenance practices, lack of surveillance on the health of tires,” says Mallesh Kumar highlighting major challenges in tire industry
Overcoming these challenges.
“Government authorities should have a periodic inspection on tires, tires more than five-year-old and with minimum tread depth (1.6mm for PCR) are not to be used, resale of old/used tires should not be encouraged, tires with cuts and injuries (which are not safe) are to be removed,” suggests Kumar.