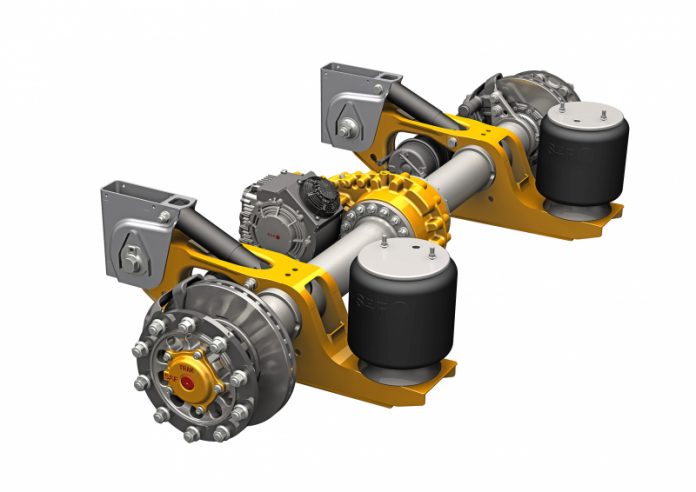
The SAF TRAKr electric trailer axle from SAF-HOLLAND is introduced on the market in stages: After the successful test phase over several years, pre-production has been in full swing in Bessenbach since June 2022. Standard production of the recuperation axle will start in 2022.
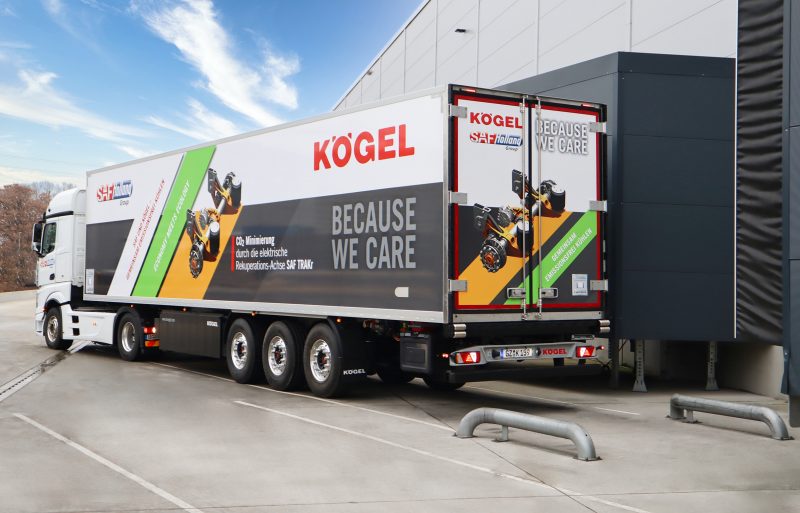
The use of electrified trailer axles is becoming increasingly important for low emis-sion transports, such as for refrigerated semi-trailers and inner-city applications. Another innovation driver for the electric technology are the legal regulations: More than 50 zero emission zones are planned in Europe for the near future, including in Berlin, Paris and London. Stricter noise pollution standards also encourage man-ufacturers to produce vehicles that are significantly more quiet. To limit global warming as planned, CO2 emissions have to be lowered by up to 95 per cent by 2050. “We see great opportunities for electrified trailer axles here: They reduce CO2 and noise emissions and meet legal requirements, for example for night-time refrigerated transports on inner city routes. The electric axles also cater to the in-dustry trend towards ‘greener transport’,” says Olaf Drewes, Director Group Inno-vation EMEA at SAF-HOLLAND.
SAF TRAKr lowers emissions and fuel consumption
The SAF TRAKr trailer axle uses regenerative braking to lower the emissions and fuel con-sumption of the overall vehicle. To do this, the centrally positioned high voltage generator unit converts the kinetic energy of the trailer into elec-trical energy. The generated energy is stored in a Li-ion battery and then used to run the electrical units in the trailer, such as the refrigeration units, on electricity alone.
The main areas of application are refrigerated semi-trailers, tank trucks and silo trailers. For the drivers, the purely electrical operation of the refrigeration unit pro-vides appreciable added comfort on the road, as they are exposed to significantly lower noise emissions. The regenerative braking axle is manufactured at the SAF-HOLLAND factory in Bessenbach in northern Bavaria. It is initially launched on the European market, before the SAF TRAKr will then also be introduced in other re-gions worldwide next year.
Easy maintenance and reliable spare parts supply
For maximum flexibility and ease of maintenance, the operating strategy and the individual components of the SAF TRAKr are perfectly coordinated. Numerous components are permanently integrated into the electric axle. This allows vehicle manufacturers to install or retrofit the SAF TRAKr with only little effort while using standard interfaces. Maintenance is also easy and cost efficient: Neither the centrally installed gearbox with the flanged-on generator nor other HV components have to be removed to uninstall wheel ends and wheels. Wear parts such as brake pads or brake rotors are identical to the components for the non-electrified SAF-HOLLAND axles. This makes the spare parts supply easier and more reliable.
SAF TRAKr: modular design offers flexibility
The SAF TRAKr uses a high-voltage generator module for electric regenerative braking, with a maximum power of 20 kW by design. The axle is designed for axle loads from nine to ten tons. It is available with different disc brakes for 19.5” and 22.5” tyres and for the SAF INTRA and SAF MODUL suspension systems. SAF-HOL-LAND is cooperating with external partners for the regenerative braking systems.
The generator runs independently of the tractor unit and only while the vehicle is in motion, but not during interventions by the ABS braking system or driving dynam-ics. For reasons of type approval, regenerative braking is currently not yet permit-ted for adaptive braking. The generator is deactivated at vehicle speeds below 15 km/h so the required start-up torque and therefore the fuel consumption of the tractor unit are not increased during these phases. Charging options are energy generation by the axle while driving (generator operation) and charging from the external power supply during standstill, for example when the vehicle is loaded or unloaded.